Service Sector
A large-scale healthcare and services company, with over 2,000 employees, sought ErgoCorp’s support to comply with an inspection conducted by the Ministry of Labor and Employment. The company was required to meet NR-17 regulations and was also experiencing high absenteeism related to mental health issues.
ErgoCorp conducted all Ergonomic Work Analyses (AETs) and implemented an ergonomics and quality-of-life management system—all within 90 days. The regulatory agency approved the documents, meaning the company was not fined, and the inspection process was closed.
We continued working with the company, implementing quality-of-life programs and workplace exercise initiatives. After six months, there was a 50% reduction in cognitive workload-related medical leave. Additionally, organizational measures were implemented, and by 2019—ten years later—absenteeism had decreased by 90% compared to 2009, when we first started working with the company.

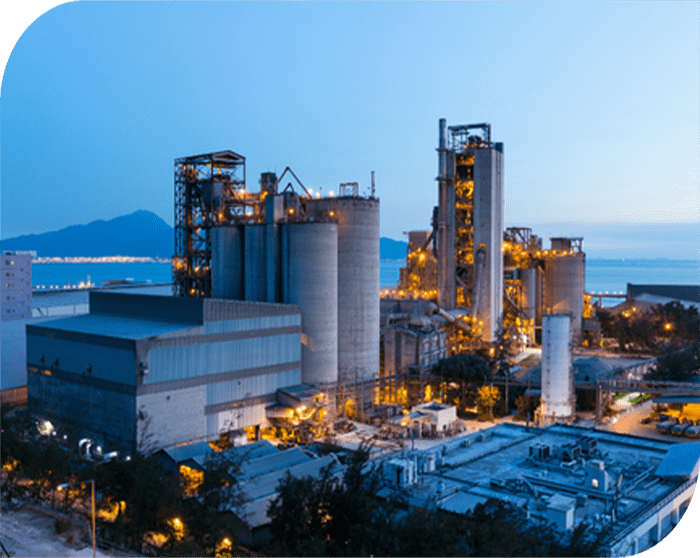
Capital Goods
An American multinational company, a global leader in its sector, sought ErgoCorp’s support in 2009 to identify the causes of musculoskeletal disorder-related absenteeism (CID:M), which was significantly impacting its operations in Brazil.
After mapping all processes through Ergonomic Work Analyses (AETs), several specific ergonomic deviations were identified, responsible for over 80% of recorded medical leaves. ErgoCorp collaborated with the company’s production engineering and project departments to develop various devices and tools that completely neutralized ergonomic risks in operations.
As a result, 15 high-risk workstations were transformed into low-risk workstations. Over the past ten years, we have continued to monitor all operational changes to ensure that process modifications and new implementations comply with all ergonomic and operational requirements.
Agribusiness
An agribusiness company, which in 2018 ranked among the top 1,000 companies in net sales and the top 400 agribusiness companies, had signed a Conduct Adjustment Agreement (TAC) in 2016 with the Public Labor Ministry. The agreement required a 1-million-real investment to address ergonomic and occupational health and safety issues.
The company turned to ErgoCorp to map all production processes, conduct Ergonomic Work Analyses (AETs), and implement a management system in record time (60 days). The ErgoCorp risk management structure supported the creation of the SSHE (Safety, Health, and Environment) Committee, which was later expanded across all company units.
After 24 months of intensive work, the company not only fulfilled the TAC agreement but also became a benchmark for the Public Labor Ministry, which now recommends its risk management model to other companies.
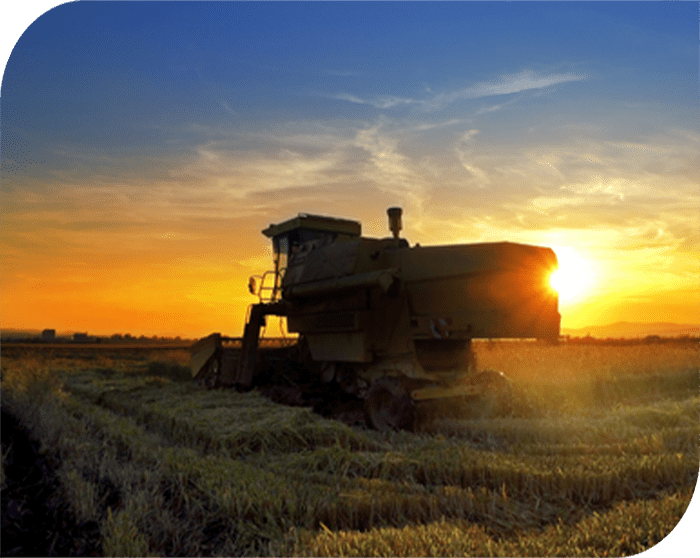
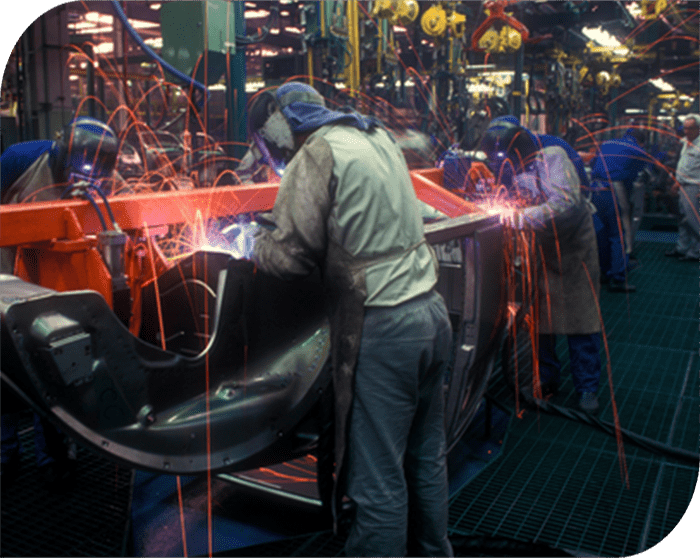
Auto Parts
A market-leading company and one of the largest auto parts manufacturers in the world, with more than 2,000 employees. Ergonomic Work Analyses, Kinesiological Evaluations, and Compatible Work Assessments (CTC) were carried out with the objective of evaluating employees with limitations in low value-added activities, allocating employees with physical limitations to compatible workstations, adapting workstations according to these limitations, and meeting the legal requirements established by NR-17 and NR-12.94 in 1,580 activities. The results were: allocation of 46 employees to compatible workstations, adding value to the company’s operations; reduction of third-party contracts through the allocation of these employees, saving 2.5 million per year; compliance with national and international ergonomic legal requirements; support for future defenses in labor claims related to occupational diseases; support for clinical evaluations by the medical department and monitoring of the company’s current labor liabilities.